Getting The Indonesia Furniture Manufacturers To Work
Getting The Indonesia Furniture Manufacturers To Work
Blog Article
Indonesia Furniture Manufacturers for Beginners
Table of ContentsSome Known Questions About Indonesia Furniture Manufacturers.Some Known Details About Indonesia Furniture Manufacturers The Main Principles Of Indonesia Furniture Manufacturers Our Indonesia Furniture Manufacturers DiariesThe Ultimate Guide To Indonesia Furniture Manufacturers
There are some disadvantages to buying from a furniture manufacturer. For one, you may have to wait longer to receive your furnishings given that it's being tailored. Additionally, you might not have the ability to see or touch the product before you purchase it. A furniture store is a business that markets furnishings made by various producers.When you purchase from a furnishings retailer, you're acquiring an item of furniture that's currently been made and prepares to be delivered to your home. One of the advantages of buying from a furnishings store is that you can usually see and touch the item before you purchase it.
At BH Furnishings, we think in setting brand-new requirements for quality in the production of industrial furniture - Indonesia furniture manufacturers. Our dedication to development has led us to welcome advanced automation technology, changing the means we produce furnishings and moving us to the forefront of the market. Gone are the days of manual work controling the production flooring
Claim bye-bye to manufacturing hold-ups and overtime costs. This implies we not only fulfill yet go beyond delivery target dates, supplying our customers with a degree of integrity that conventional production methods merely can't match.
Some Known Factual Statements About Indonesia Furniture Manufacturers
Our manufacturing capability has risen, permitting us to fulfill the demands of also the biggest projects without endangering on quality. As your partner in industrial furnishings services, we can effortlessly scale our result to suit your needs, regardless of the scale. While conventional manufacturing counts greatly on hand-operated labor, our automated systems have substantially minimized our dependence on a big labor force.
Furniture manufacturing is an intricate process that entails different phases, from designing and product selection to manufacturing and setting up. At each phase, there is an opportunity of defects or mistakes that can endanger the high quality of the last item. To make sure that furniture is of premium quality, furniture manufacturers implement quality control processes to determine and rectify any kind of concerns that may arise during production.
The evaluation process should cover various aspects, such as setting up, coating, colour, layout, product packaging, labelling, and marking. By carrying out a strenuous assessment procedure, manufacturers can guarantee their products meet the essential quality, security, and sturdiness demands. They likewise supply the flexibility to address concerns and make corrections prior to completing the final item.
Furnishings top quality requirements are sets of standards and needs for furniture manufacturing. They specify the called for high quality degree of look at this website furniture manufacturing and cover facets such as safety, longevity, strength, and ecological impact.
How Indonesia Furniture Manufacturers can Save You Time, Stress, and Money.

To ensure their furniture items can endure numerous weather condition aspects, consisting of sun, rain, snow, and wind, producers should take into consideration worldwide acknowledged criteria that consist of assessments and testing. Right here are several of the standards to bear in mind: ASTM F1561-03 is a global basic developed by the American Section of the International Organization for Screening Products (ASTM).
UL 962 is a worldwide safety criterion created by Underwriters Laboratories (UL), an independent international supply safety remedies company. The typical applies to home and commercial furnishings, consisting of outside furniture.
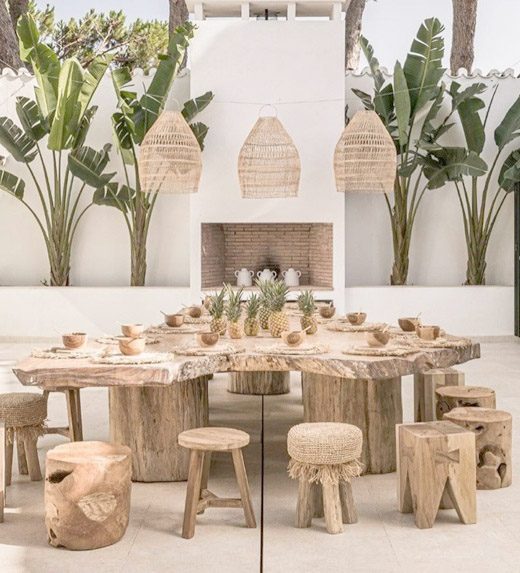
The Ultimate Guide To Indonesia Furniture Manufacturers
It helps to determine defects in the furniture and review its performance and conformity with the called for quality criteria. Here are the actions for performing laboratory screening for furniture: Producers gather samples of furniture parts that call for testing. These examples normally represent the different types of furniture that they create.
This may include a mix of various examinations, consisting of strength screening, toughness screening, security screening, and ecological effect testing. The samples are then examined for various top quality parameters, such as toughness, durability, safety and security, and environmental effect. The outcomes are after that examined to establish whether the products meet the needed top quality criteria.
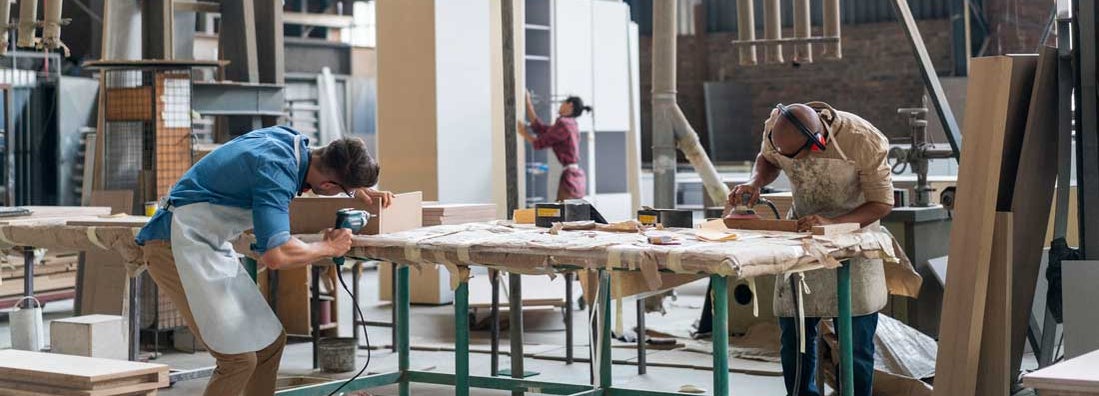
Typically, every retail store furniture is various. over here Layouts conference client convenience Making best use of room usage in storage, display, step, guest seats and walkways Ensuring simplicity of access to items for tests and acquisition Designing modular furnishings that is simple to relocate and recondition Satisfying safety needs of consumers A fast TAT from layout to manufacturing and installation with minimal mistakes can assist resolve the above issues.
Some Known Details About Indonesia Furniture Manufacturers
Also, a designer can understand the marketplace fads and be Get the facts prepared with innovative designs in advance. Read right here: How DriveWorks Aids You to Minimize Lead Time in Production Designers usually have to transform the shapes and sizes of furniture at a moment's notice. These may have different visual and practical needs like front workdesk, and maintenance workdesk that differ in measurements.
Enhances product top quality and minimizes scrap. Field guideline documents along with quantity departures are also produced for retail store furnishings installments. Layout models and disputes are reduced, and the store flooring can begin producing on the day of sales.
It is an extremely competitive market, with services making every effort to keep up with altering consumer needs and the most current technological trends. Today's customers are much more most likely to prefer furnishings that is tailored and made with lasting materials.
Report this page